The impact of the Internet of Things (IoT) on industries worldwide has been revolutionary, transforming the way businesses operate, innovate, and grow. In plastic injection molding, the influence of IoT is increasingly evident.
Traditionally known for its emphasis on efficiency and precision, plastic injection molding is now experiencing a significant shift towards unparalleled efficiency, quality, and sustainability with the integration of IoT technologies.
By incorporating IoT into injection molding processes, companies are taking considerable steps towards a new era characterized by real-time data collection and analysis through embedded sensors and networking capabilities in machines.
This enables predictive maintenance, remote monitoring, optimization of energy usage, and overall transparency in production. As a result, waste reduction, minimized downtime, and enhanced product quality become achievable goals throughout the entire manufacturing process.
From local medical plastic injection molding companies to global commercial industries, the IoT is reshaping what’s possible in the world of plastic injection molding. It brings about increased responsiveness to market demands while promoting sustainability and profitability.
This article aims to explore various impacts that IoT has introduced to this evolving industry by shedding light on both challenges faced and opportunities presented to businesses.
Table of Contents
The Convergence of IoT and Plastic Injection Molding
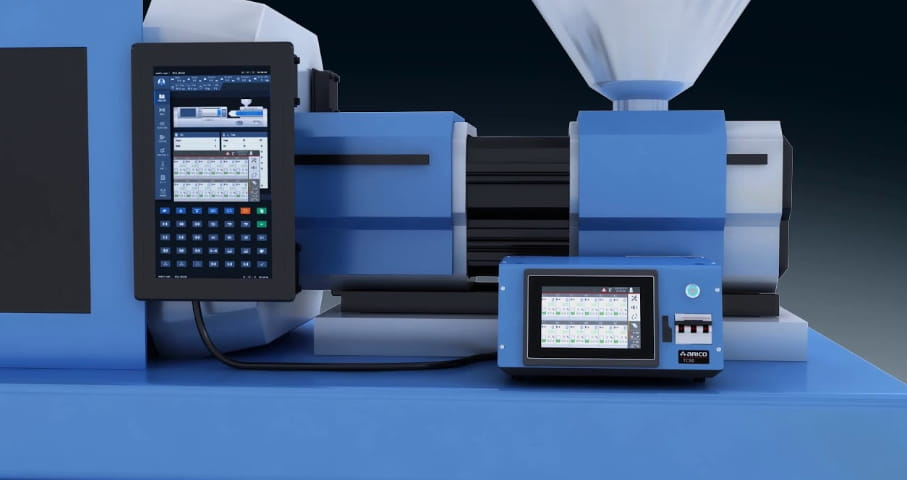
The Internet of Things (IoT) is rapidly revolutionizing the manufacturing industry. It creates an interconnected ecosystem where machines, devices, and humans can seamlessly communicate with each other.
IoT involves integrating sensors, actuators, and network connectivity into machines and equipment to enable real-time data collection and analysis. By adopting this data-driven approach, manufacturers can use predictive maintenance techniques to identify potential issues before they escalate into equipment failures.
Real-time monitoring through sensors embedded in molding machines enables tracking of crucial parameters like temperature, pressure, and cycle time. By analyzing this data, dynamic adjustments can be made to uphold optimal operational conditions and ensure top-notch product quality.
Ultimately, this reduces downtime and minimizes maintenance costs. IoT technologies also assist manufacturers with precise control over their production processes, thereby enhancing efficiency and ensuring superior product quality.
As customization, rapid production cycles, and sustainability rise in importance in today’s world; IoT proves instrumental in helping manufacturers efficiently meet these demands. Integrating IoT into plastic injection molding not only optimizes current practices but also encourages an adaptable, responsive, and sustainable future for this industry.
Benefits of Integrating IoT in Plastic Injection Molding
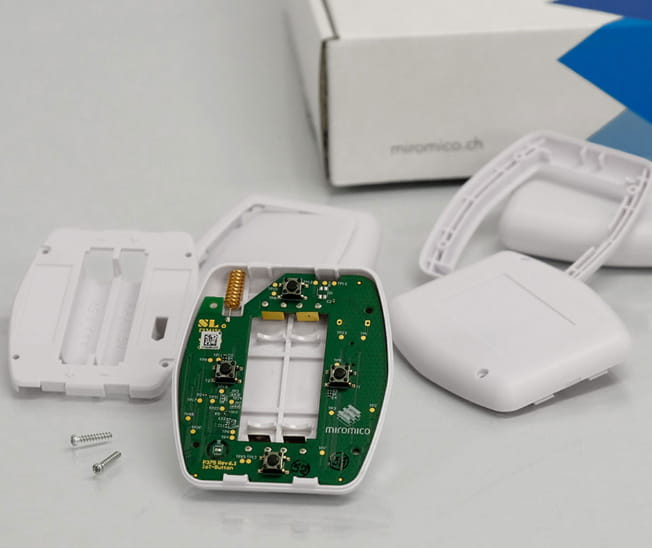
Integrating IoT technology into plastic injection molding provides numerous advantages. These benefits enhance efficiency, consistency, and cost-effectiveness in operations.
1. Real-time Monitoring and Feedback:
IoT sensors embedded in injection molding equipment enable real-time monitoring of key parameters. These include temperature, pressure, and cycle time. The continuous flow of data offers instant feedback, empowering operators to swiftly identify and address any issues as they arise.
By allowing proactive adjustments, real-time monitoring optimizes operations while minimizing the need for costly and time-consuming corrective actions after problems have occurred.
2. Predictive Maintenance and Reduced Downtime:
IoT technology has the ability to predict equipment failure in advance by analyzing data trends and identifying irregular patterns. This proactive approach to maintenance is highly valuable as it allows for timely servicing of parts before they experience any issues.
By preemptively detecting and resolving problems, manufacturers can avoid unexpected and expensive downtime, ensuring continuous and efficient production.
3. Enhanced Quality Control and Consistency:
IoT ensures that every part produced meets precise specifications and the highest standards expected. By continuously monitoring machine parameters and product characteristics, real-time adjustments can be made to prevent any potential defects.
This meticulous level of control leads to consistent, top-quality products, which is crucial in maintaining customer trust and satisfaction.
4. Efficient Resource Management:
IoT technology assists injection molding companies in optimizing resource utilization. By continuously monitoring real-time energy consumption and operational costs, these companies can identify areas for improving efficiency.
This may involve adjusting machine settings to minimize energy usage or reorganizing workflows to avoid bottlenecks. Enhanced efficiency not only leads to cost savings but also contributes to more sustainable operations by reducing waste and overall environmental impact.
Challenges and Considerations
Although the incorporation of IoT in plastic injection molding has many advantages there are some challenges and considerations that manufacturers must address.
1. Concerns about Data Security and Privacy:
As IoT devices gather and transmit large amounts of data, ensuring the security and privacy of this information becomes crucial. The data can contain sensitive content, such as proprietary production parameters or customer-specific designs.
If unauthorized individuals gain access to this data, it could result in intellectual property theft or sabotage, underscoring the necessity for robust cybersecurity measures.
2. Initial Setup and Investment Costs:
Implementing IoT technologies in plastic injection molding requires a significant initial investment. This includes the expenses on sensors, networking hardware, software platforms for data analysis, and possibly upgrading existing machinery to enable IoT compatibility.
For smaller manufacturers, this upfront cost can pose a major entry barrier, emphasizing the need for careful consideration of the return on investment.
3. Training and Adapting to New Technologies:
The implementation of IoT technologies in manufacturing requires a skilled workforce capable of operating, maintaining, and interpreting these systems.
However, this transition comes with challenges. Training current employees or hiring new personnel proficient in IoT can be both time-consuming and costly.
Moreover, the incorporation of IoT often necessitates significant adjustments to established workflows and processes, which might encounter resistance from staff accustomed to traditional methodologies.
Case Studies: Successful Implementations
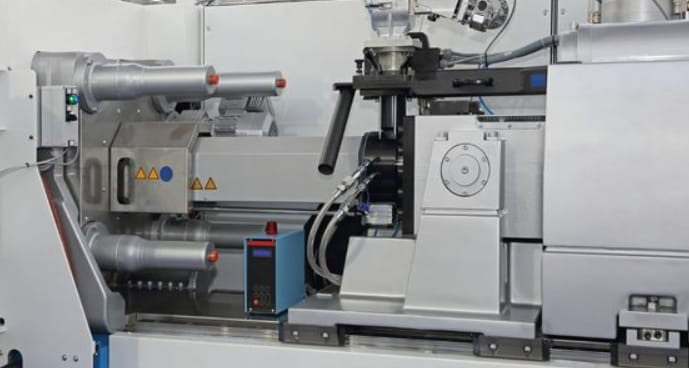
Nicolet Plastics LLC:
Nicolet Plastics LLC provides comprehensive mold design and manufacturing services to various industries. To optimize its production process, the company uses IoT technology. By installing sensors on its molding machines, Nicolet Plastics can continuously monitor critical parameters like temperature, pressure, and cycle time.
This real-time data is analyzed to make immediate adjustments, ensuring optimal operating conditions and the highest product quality. As a result of these efforts, Nicolet Plastics has observed a 20% reduction in defective products and a 15% improvement in overall production efficiency.
These improvements not only help reduce waste but also significantly lower production costs, enhancing Nicolet Plastics’ competitiveness in the market.
Murray Plastics:
Murray Plastics, located in Gainesville, Georgia, brings a wealth of experience to plastic part production. By integrating IoT into their operations, the company has implemented predictive maintenance strategies. These strategies involve sensors detecting machine component wear before critical failure occurs.
This proactive approach significantly reduces unexpected downtimes and allows for more consistent production schedules. The results speak for themselves; within the first year of IoT integration, Murray Plastics reported a remarkable 25% reduction in maintenance-related downtime and a noteworthy 10% decrease in maintenance costs.
Furthermore, this IoT integration has led to more efficient energy usage, resulting in an impressive 15% reduction in energy costs.
Conclusion and Future Outlook
The future of IoT in plastic injection molding looks great as technology continues to evolve. One exciting development is the emergence of machine learning algorithms that can analyze the large data streams from IoT sensors.
These algorithms enable highly precise and timely adjustments to equipment settings, optimizing production outcomes.
Moreover, we can anticipate a growing trend towards interconnected and collaborative manufacturing environments where IoT devices throughout the supply chain communicate with each other, streamlining the entire production process.
As sustainability becomes increasingly important, IoT has the potential to play a key role in developing “smart” factories that maximize energy efficiency and minimize waste.
In today’s competitive landscape, integrating IoT into plastic injection molding goes beyond being a mere trend. It is now essential for companies striving for excellence, sustainability, and a competitive edge in this rapidly evolving market.